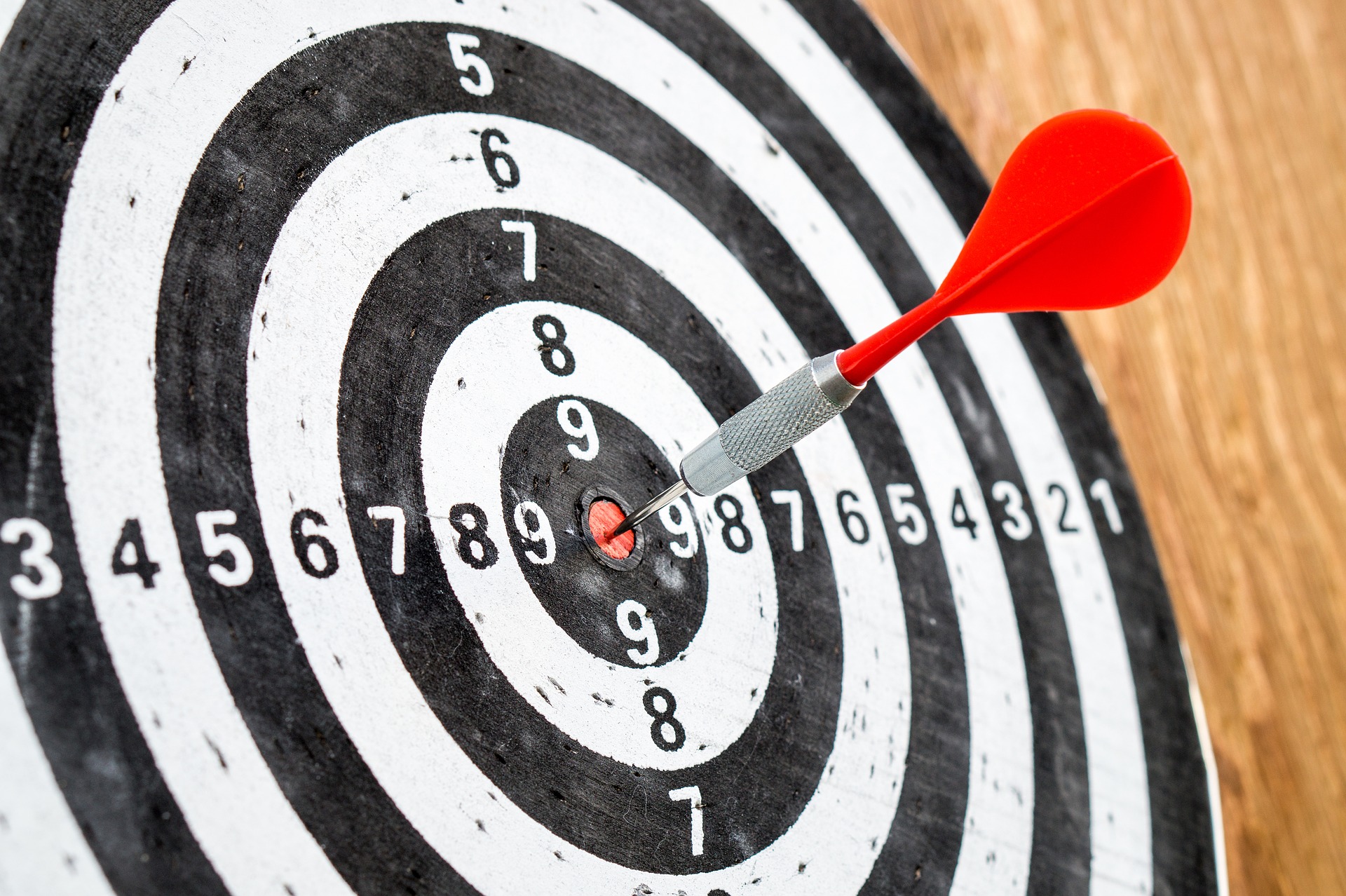
When monitoring heat, for example, a 1°F error from your measurement system could be costing your company thousands of dollars every year. What if you could cut $15K in spending annually with minimal effort?
Quick Definition Review
Accuracy, Precision and Resolution:
The quality of the instruments and the equipment you’re using can have a major impact on your company’s finances. Therefore, the accuracy and precision of your sensors’ measurements are key quality factors to look for when it comes to purchasing instrumentation.
Although accuracy and precision are often used interchangeably, in the test and measurement industry, they are two of the main factors that come into play when evaluating a sensor’s quality.
Accuracy refers to how close the measurements are to the true value while precision refers to how close measurements are to each other.
On the other hand, resolution is the smallest number than can be indicated or recorded by an instrument.
In short, accuracy is a combination of precision, resolution and calibration. As we will see in the following case study, a slight error in accuracy caused by an uncalibrated sensor can have a significant impact on a system’s overall performance.
Typical Case Study
Here’s a typical example of a problem you may encounter:
Water is used for heating, flowing at a rate of 100 gallons per minute (GPM) for a year. The water is to be controlled at 100°F, but due to the monitoring sensors’ inaccuracy, it’s actually being controlled at 101°F. How much heat is used to raise the temperature of a year’s worth of fluid by 1°F and how much does that energy cost?
Q=cpm (delta T) Where:
Q = heat transferred (BTU)
cp = specific heat at constant pressure (BTU/lbm-°F)
m = mass (lbm)
(delta T) = temperature change (°F)
cp = 1 BTU/lbm-°F
m = (8.33 lbm/gal)(100gal/min)(525600min/yr) = 437,824,800 lbm/yr
(delta T) = 1 °F
Solving: Q = 437,824,800 BTU = 128,282 KW-hour
For an electrically heated system:
Assuming the cost of electricity is 12 cents per KW-hour.
Cost = (128,282 KW-hour)(0.12 dollars/KW-hour) =
$15,393.84/year from a 1°F error
How You Can Avoid This Situation
As you can see, a small error can end up costing a lot of money.
The first step to avoid these situations is to choose a high quality sensor that matches the requirements of your application. When it comes to instrumentation design, the most fundamental aspect is eliminating or minimizing variables that cause inaccurate measurements. Making sure that you choose a sensor that is adapted to the environment in which it will be used — i.e. indoor, outdoor, in contact with water or corrosive substances, etc. — and that it is properly installed are two of the many elements to take into consideration.
The second step to ensure that the accuracy and precision of your device is regular maintenance through calibration. Calibration is the process of configuring an instrument to provide a result for a sample within an acceptable range. It is typically performed to determine the error or verify the accuracy of the device under test’s unknown value.
The frequency at which your instruments should be calibrated varies depending on the manufacturer, the type of instrument and what it’s used for. A general recommendation is to have them recalibrated once a year, though your manufacturer may suggest otherwise.
Want to find out more about calibration? Check out our demo videos on our YouTube channel for Float level sensor calibration, Pressure sensor calibration and Capacitive level calibration.
https://www.youtube.com/watch?v=c5-UauwuJis
(to make your selection, click on a regional language)
![]() Canada |
![]() USA |